Construction's Deadliest: The Top 5 OSHA Violations (and How to Avoid Them)
- Missy England
- May 8, 2017
- 3 min read
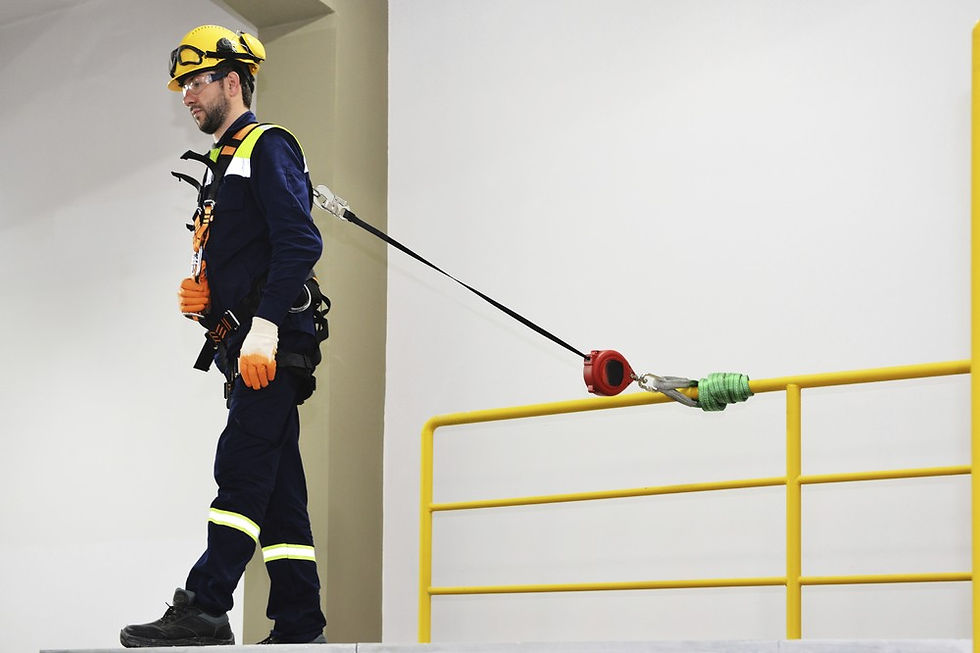
Lack of fall protection and improper use of scaffolding contributed to nearly 40% of construction fatalities in 2014. While the industry voices concern over the high fines for these violations, the damage is far greater than any amount of money. For construction businesses and their staff, there’s continual risk of death or injury associated with the job, as well as the risk of lost productivity and delayed schedules.
The top 5 most frequently cited OSHA violations across all industries in 2015 were:
Fall Protection
Hazard Communication
Scaffolding
Respiratory Protection
Lockout/Tagout
The real cost of safety violations.
When it comes to the monetary implications, the cost of safety violations is steadily increasing. Until recently, OSHA fines have been small compared to the fines imposed by other federal enforcement programs. The recent change comes from the latest federal budget bill permitting OSHA fines to emulate inflation.
Safety experts for both the industry and labor markets predict violations will increase 78%. To give you an idea, the maximum fines (for the worst violations) were previously $70,000 and will be increasing to $125,000, while lesser violations will increase from $7,000 to $12,500. OSHA must adjust the fines before August of this year.
While falls in the workplace represent the majority of fatalities in this industry, the statistics show just how overpowering their effects are on the industry’s total death toll. While falls accounted for 39.9% of fatalities in construction during 2014, electrocutions, struck by object, and caught in-between claimed 18.3% together, or less than half of the number killed by falls. Taken together, these four accident types are called construction’s “Fatal Four.”
Understanding the Standards
OSHA recognizes that falls usually result from complex dynamics, so preventing them means dealing with both human and equipment issues. The recipe for reducing falls in the workplace is in OSHA’s Subpart M booklet. The logical place to start in reducing your chances of workplace falls is by becoming familiar with these provisions. But even before focusing on the rules and guidelines for preventing falls, fostering awareness can get your organization off to a good start.
Stand-down for Safety
OSHA holds the National Safety Stand-Down to Prevent Falls in Construction every May which, last year, involved more than 2.5 million workers. The idea is to involve employees by conducting toolbox talks on fall prevention, performing safety equipment inspections, developing rescue plans, discussing job-specific hazards, and creating awareness of the importance of workplace safety. For tips on hosting a successful stand-down, check out this article by the U.S. Department of Labor.
Don’t “fall” short
To get the best results, you should continue to build awareness throughout the year. Besides periodic safety meetings where you highlight particular fall dangers related to each job site, regular training is also important. OSHA recommends keeping training sessions short and easy to follow and encourage participation with questions and discussions.
Ideas to foster involvement include:
Ask attendees questions about potential fall hazards on the current work site
Ask attendees to share experiences they’ve had, or have witnessed that illustrate how easily and quickly falls occur
Bring up a recent news story related to a construction accident involving a fall and use it to open the subject ––which helps attendees focus on the project
Consider using the OSHA Prevention Videos to augment training times
Create a culture of safety in the workplace.
Observations of organizations with lower-than-average injury and illness rates, (as well as independent research,) have confirmed that a safety culture will reduce incidents more than any other process you might use.
A company with a culture of safety will make everyone feel responsible for safety outcomes and will aggressively find and mitigate unsafe conditions and behaviors throughout the organization. In an environment like this, everyone is empowered so that any worker can feel comfortable reminding a project manager to wear safety glasses, or a CEO to put on a hard hat when on the job site. It’s also common for coworkers to look out for each other by pointing out safety oversights, or working as a team to correct safety issues.
There’s still work to be done
Two of the top 5 OSHA violations weigh heavily on the construction industry though, and the increasing fines for those violations remind us that there is work still left to accomplish. But with knowledge, continual awareness, training, and cultures of safety, any construction business has a better chance of maintaining safe place to work.
Comments